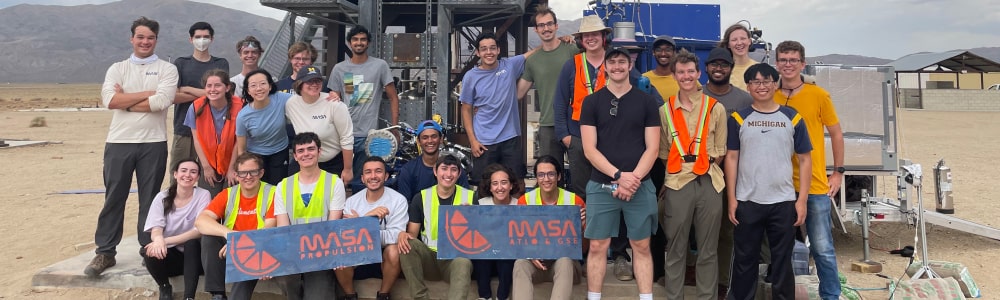
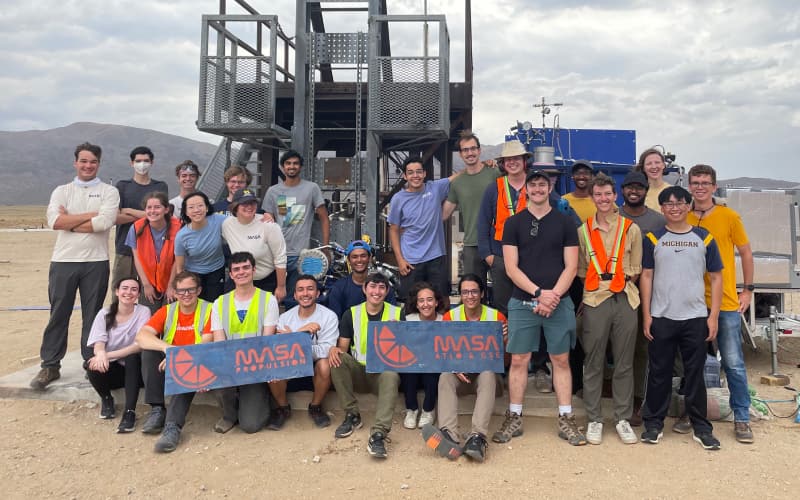
Pictured: MASA members pose for a photo after a successful hotfire of the RP-D2 engine in July 2022
Who is MASA and What is Liquid-Propellant Rocketry?
Written By Michigan Aeronautical Science Association
MASA, the Michigan Aeronautical Science Association, is the student-run rocketry team at the University of Michigan. We take a multidisciplinary approach to engineering, bringing students together to design, build, and launch pioneering liquid-fueled rockets. MASA is composed of 7 subteams, allowing team members to grow in all aspects of engineering, business, outreach, and leadership. Together, MASA works to take Michigan to new heights!
In 2018, we were the first team to launch a liquid-propelled rocket for the Spaceport America Cup, and we have since been working to continue breaking records. Our current project, Clementine, utilizes state-of-the-art avionics, aerostructures, and propulsion systems as part of what will be the largest student-built rocket to launch in the United States!
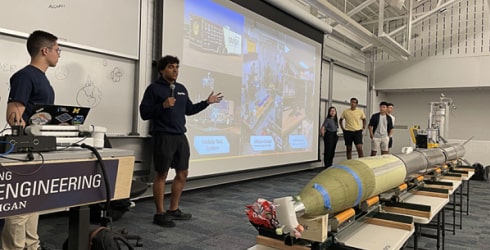
Pictured: A prototype structural assembly of MASA’s Clementine rocket on display at the team’s Fall 2022 recruitment meeting
What Is A Liquid-Bipropellant Rocket?
“A liquid-bipropellant rocket is one that generates thrust by combusting a liquid fuel (often a form of kerosene, methane, or hydrogen) with a liquid oxidizer (often liquid oxygen).”
Liquid-bipropellant rockets are generally the most complex class of rocket to develop because they require extra valves, sensors, propellant tanks, control systems, and avionics hardware that are not needed for simpler solid-propelled rockets. However, liquid-bipropellant rockets are much more versatile and efficient, and the added challenge allows us to grow as engineers! To give you a taste of rocket science, we will discuss our design process and how we choose materials to accomplish our goals in this article.
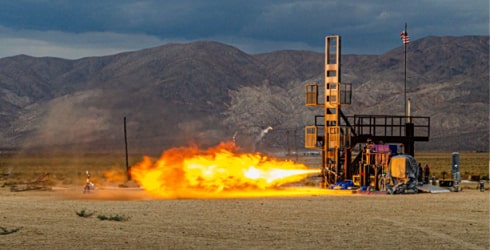
Pictured: A still image taken from MASA’s July 2022 hotife of the RP-D2 engine
What Materials Are Used in a Liquid Bipropellant Rocket Engine?
When building our rocket engine, we consider materials very carefully based on required function, operating environment, and our engineering analysis of applied loads. Some key areas where Online Metals is able to support us are on our engine’s inner liner, outer jacket, and injector. Our engines are less complex than pump-fed engines that are used in industry, but are plenty sophisticated in their own right - MASA has built and tested engines that produce over 2,000 lbs of force!
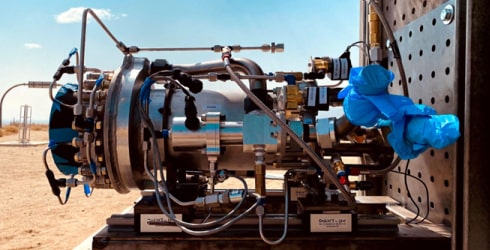
Pictured: MASA’s RP-D2 Engine on the Reaction Research Society’s test stand at the Mojave Test Area
The inner liner of one of MASA’s engines is subject to high temperatures (over 700 °F) on the inner “hot-wall” and room temperature conditions on the outer “cold-wall”. Copper has a high thermal conductivity, which helps limit the thermal stresses caused by the temperature gradient across the inner liner.
The outer jacket is a second component that wraps around the inner liner. We flow liquid kerosene through the gap between the inner liner and outer jacket, which allows the engine to operate continuously without an excessive temperature increase. Our outer jacket is made out of Aluminum 6061 due to its high strength-to-weight ratio at room temperature, versatility, and availability.
Before combustion can occur inside of our engine, we flow our propellants through the injector to ensure better propellant mixing and more efficient performance. Our injector is built out of Stainless Steel 316 because it is less likely to react with liquid oxygen, and maintains strength at high temperatures better than most comparable metals.
Before qualifying for use on our rockets, our engines undergo a rigorous testing campaign of at least several months in length. Each engine’s test campaign begins by flowing water and liquid nitrogen through the individual valves and tubing assemblies that bring propellants from our tanks to the engine. Each test provides meaningful data about pressure drops and flow rates which are used to make improvements to the system. Once our team is happy with the characterization of these valves and tubing systems, we step into full system-wide tests of the engine. These tests culminate in a hotfire testing campaign, during which we secure our engine in-place and fire the engine just as we would during flight! Our hotfire tests often produce thousands of pounds of force, loud noise & stunning visuals, and a lot of adrenaline!
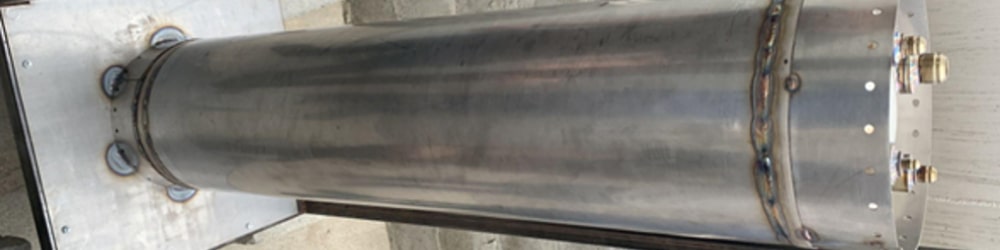
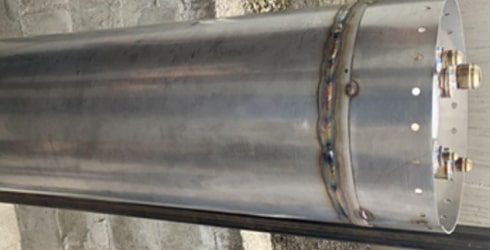
Pictured: A prototype liquid oxygen tank for MASA’s Clementine rocket
How are Liquid Propellant Tanks Built?
MASA’s propellant tanks store the rocket’s pressurized liquid fuel (RP-1, which is a refined kerosene) and oxidizer (liquid oxygen) at over 400psi. Our tanks need to survive these pressure loads, as well as aerodynamic and inertial loads during flight. Because our propellant tanks are fully welded structures that require high strength, we use the Stainless Steel 304 alloy for each tank.
MASA’s propellant tanks are composed of a tube section, two endcaps, two coupling rings, and a set of weld-on bung fittings to which we attach propellant tubes and various fluid components. Some of our propellant tanks also have auxiliary components including bung adapters, anti-vortex baffles, and anti-slosh baffles.
The tubes of our propellant tanks are manufactured by rolling a sheet of Stainless Steel 304 into a tube shape, and welding the seam. Our endcaps begin as COTS (commercial off the shelf) pipe endcaps, and are CNC (computer numerical control) machined down to the desired geometry. This geometry includes several holes in each endcap where the bung fittings are welded in place, and a groove where our coupling rings are welded in place. Finally, each endcap assembly is welded to the tube section, creating one full tank. Some of our tanks contain additional components to facilitate welding of the bungs, or prevent dangerous dynamic phenomena such as vortex formation and propellant sloshing. These components are generally cut and/or machined in-house, and then welded in place on the full tank assembly.
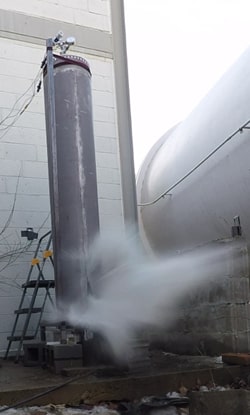
Pictured: A still image from a destructive hydrostatic burst test of a prototype propellant tank
To mitigate the safety hazards associated with pressure vessels, we perform extensive testing prior to qualifying a propellant tank for flight. We first begin by fabricating a prototype flight propellant tank, and performing a destructive hydrostatic burst test. The tank is filled with water, and then pressurized until the tank bursts — our most recent prototype burst at 780psi! If the results of the destructive test align well with our design and analysis intent, we go forward with manufacturing of our actual flight propellant tanks. After passing a successful non-destructive hydrostatic pressure proof test, our flight propellant tanks are officially qualified for flight.
How does the Rocket Airframe Work?
MASA’s current rocket, Clementine, has some metallic airframe sections and some composite airframe sections. The airframe makes up the visible exterior of the vehicle, and needs to withstand significant aerodynamic and thrust loads. Several airframe sections also have holes and cutouts on them to accommodate tubing, fluid components, and provide access to the interior of the rocket. These holes and cutouts are carefully analyzed, to ensure that the airframe maintains adequate strength and stability despite them.
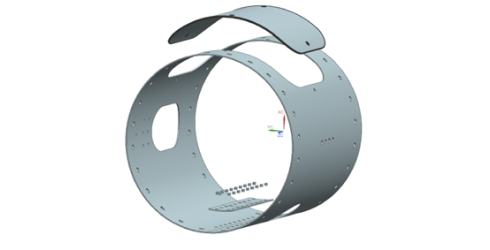
Pictured: An exploded view CAD render of the Clementine rocket’s inter-tank airframe
MASA’s metallic airframe sections are made of Aluminum 5052, due to its availability and formability. Each airframe section starts as a sheet of Al-5052 that is laser cut to the desired geometry. The sheet is then rolled into a cylindrical shape, and held together via a backing plate and set of fasteners (see image above). The aluminum airframe sections are reliable, relatively cheap, quick to prototype and iterate, and easy to analyze.

Pictured: MASA’s composite fiberglass nosecone with its titanium tip attached
MASA also utilizes some fiberglass-based composite airframe sections to house electronic hardware components. Fiberglass is RF-transparent, meaning that telemetry* can be maintained between the rocket’s flight computer and the ground station at the launch site. Our composite airframe sections are manufactured by manually laying up epoxy-soaked fiberglass sheets over a foam mold. This manufacturing process requires practice, but our team has become comfortable with it after developing several prototype articles.
Some of MASA’s airframe sections, especially the composite sections, are difficult to analyze in traditional ways. For instance, the anisotropicity* of the composite airframe sections requires different analysis methods and tools than those required for the metallic airframe sections. To ensure that our hardware is meeting the standards necessary for flight, we test our airframe sections with a hydraulic press in a lab on campus. This test data is critical for understanding how our airframe sections will perform during flight, and for improving our analysis methods on future iterations.
Oxford Definitions (*):
Telemetry: the process of recording and transmitting the readings of an instrument.
"measurements will be transferred by radio telemetry to the shore station"
Anisotropicity: (of an object or substance) having a physical property that has a different value when measured in different directions. A simple example is wood, which is stronger along the grain than across it.
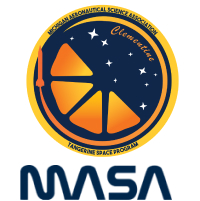
About the Featured Experts
Michigan Aeronautical Science Association (MASA)
https://masa.engin.umich.edu/
MASA is the student-run rocketry team at the University of Michigan. MASA’s new Clementine rocket utilizes groundbreaking technologies including seam-welded propellant tanks, a regeneratively-cooled engine, live in-flight telementry, and full-parachute recovery. Follow MASA on our journey to launch in May 2023!
About Online Metals
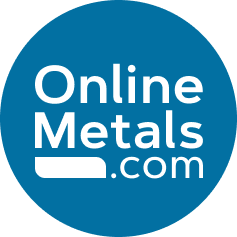
Online Metals is the world’s leading eCommerce metal supplier, specializing in small quantity cut-to-size metals and plastics, delivered in a fast and reliable manner.
Since 1998, Online Metals has expanded our catalog to over 85,000 different cut sizes, grown our national footprint to seven pickup locations across the U.S., and continued to improve upon our best-in-class customer experience.
Check out our materials: Alloy Steel, Aluminum, Anodized Aluminum, Beryllium Copper, Brass, Bronze, Carbon Steel, Copper, Cast Iron, Nickel, Nickel Silver, Plastic, Stainless Steel, Titanium, Tool Steel, Unistrut®, Wrought Iron, & Zinc
Shop by shape: Bars, Tubes, Sheets, Plates, and More.
Can't find what you're looking for? Submit a quote or contact our support team.